PDFファイルの表示はこちら。
キリンビール㈱の100%出資構成会社として、キリングループにおける酒類事業・飲料事業の一翼を担うキリンディスティラリー㈱は、年々多種多様化する製品の原材料発注業務の負荷の高まりに対して、㈱ローゼックの生産販売統合システム「Craft Line(クラフトライン)」を活用することで、従来の6分の1まで業務時間の短縮を図ることができたという。その驚くべき改善成果について、関係者に聞いた。RTDの主要生産工場
2013年6月に世界文化遺産に登録された富士山の麓、富士御殿場に同社工場はある。広大な森と年間を通じて発生する霧によって浄化される空気、そして約50年という長い歳月をかけてろ過された「富士の伏流水」が製品作りの命だ。
モルトウイスキーとグレーンウイスキーの仕込みからボトリングまでを一貫して行う世界的にも珍しい蒸溜所として、国産ウイスキーである「富士山麓」「ロバートブラウン」などのロングセラー製品を出荷し続ける一方、02年にキリンビールの100%出資構成会社となり、キリンディスティラリーと社名を変更してからは、工場を順次拡大して缶チューハイ(Ready To Drink、以下RTD)やアルカリイオン水、また中国酒など、取り扱う酒類・飲料のジャンルも急増した。
近年、購入してそのまま飲める缶入り飲料などを含めたRTDの需要が高まり、キリンビールの製品でもヒットに伴いラインアップが急拡大。RTD市場のメジャーブランドとなっている同社の「キリンチューハイ氷結」も、発売当初の2種類から現在の14液種(サイズバリエーションを含めて31容器種)に、また「キリン本搾りチューハイ」は7液種10容器種に、「キリンチューハイビターズ」は5液種6容器種になるなど、成長が著しい(15年4月現在)。
同社工場は比較的小ロット対応の製造ラインを備え、小回りが効くという特徴を持つことから、グループにおけるRTDの主要生産工場に位置付けられている。
発注業務スタッフの負担
多品種化に対応するというミッション。さらにもう一つ、同社には大きな課題が与えられている。それが、原材料や製品の在庫を適正に保つための、いわゆるジャスト・イン・タイムによるSCM体制だ。工場はブランドオーナーから送られてくる細かい需給変動に応じた製造量や製造タイミングの修正変更指示に対して、柔軟に対応し続けなければならない。また、原材料によって納品リードタイムが異なるため、製造計画は最長リードタイムに合わせる必要がある。季節限定品を含め、特定の製品にしか使用しない原材料や資材は、余分に持つことはできない。そして何よりも、1種類でも原料がそろわなければ製造ができない。製造ラインの停止は、現場作業だけでなく、物流や営業にも多大な影響を及ぼしかねない。従って、原材料や資材の発注業務を行うスタッフは、情報の正確な把握と発注の的確な判断が求められる。
飲料生産部の山田正貴部長は「多品種化とジャスト・イン・タイムの体制により、発注業務はより複雑化、細分化され、担当スタッフの負担はひたすら増すばかりでした。しかも、たとえ小さな発注ミスでも製造スケジュールに大きな穴をあけてしまう結果になりかねないので、毎日、精神的にも本当につらかったと思います」と振り返る。
業務の属人化
発注業務は①壜製品原材料(ウイスキー、中国酒ほか)②RTD製品原材料③壜製品資材④RTD製品資材――に分けて専任のスタッフが行っている。現在、RTDでは製品種別で平均約20アイテム/月(容器サイズ別を除く)を取り扱い、この一つ一つに3~15種類の原材料を使用する。スタッフは、製造計画を基に必要な原材料または資材の手配計画をまとめ、サプライヤーに発注するための納入指示書を作成する。従来、これら一連の作業は全てエクセルで行っていた。
「それこそシステム会社さんからお褒めの言葉を頂くほどエクセルを使いこなしていました。こんな機能があるのかというようなものも活用していたと思います。ですが、新しいアイテムが増える度に多くのシートやブックの数式、リンクを修正変更し、出力結果に対して横断的に一つ一つ目視でエラーを確認するという状態でした。その上、発注業務は明日に引き延ばせませんので、遅い時間まで残業しなければならない日も多くなりました」(飲料生産部 SCM担当 村上真澄チームサブリーダー)
動作が軽く、プログラミングの知識がなくても便利に使えるエクセルだが、長い運用でデータ量が増加し、マクロ計算式が複雑化すれば、どうしても処理速度は低下してしまう。結果、同社でも「入力作業中に『強制終了』になったことがありました」(同)という。
そして、そもそも発注業務は入出力作業だけで済むものではない。例えば、発注してから工場に届くまでのリードタイムや物流上の制約、ロット単位、消費期限など、それぞれの原材料や資材に関わる「固有の事情」を認識していなければならないし、急な変更への迅速な対処法などについても、多くの経験値が必要になる。結果的にはイレギュラーな処理も多くなってしまうため、決して簡単に代わりが務まる業務ではない。これは、まさに「業務の属人化」という壁である。
「特に製造計画の急な変更は頻繁に発生します。1日に数回ということもあります。しかも、その変更はランダムで、1日のうちにいつ何度告げられるか分かりません。そのたびにエクセルのシートを組み直さなくてはならず、担当スタッフはずっと気が休まりません。従来の方法では、現況や固有の事情を共有できる仕組みもないので、業務を分散したくても事実上、不可能だったのです」(飲料生産部 SCN担当 原篤氏)
かゆいところに手が届く
こうした課題に対する抜本的な改善に乗り出したのが11年11月。同社内のエンジニアリング部の協力を得ながら、担当スタッフの要望を約半年かけて整理し、RFP(提案依頼書)を作成、ソフトメーカー3社にプレゼンテーションしてもらった。その結果、「かゆいところに最も手が届くシステム」(村上サブリーダー)として、ローゼックの生産販売統合システムであるクラフトラインを翌年5月に選定した。
「確かにお金を掛ければそれなりのシステムは組めると思いますが、比較的低価格で導入しやすく、それでいて現場視点で『あればいいな』という機能がそろっていたというのが、選定させていただいた主な理由です」(同)
クラフトラインは、生産管理や販売管理、在庫管理、受発注管理、トレーサビリティ、原価計算などの各種機能を組み込むことができる食品製造業向けの統合型システム。機能でかつ工場の業務を統合的に管理できるシステムでありながら、どのような事業規模・業態でも柔軟に対応できるよう設計されているのが大きな特徴だ。このため、比較的小規模な食品工場でも導入が進んでいる。
同システムにログインすると、工場で発生した異常値や実績値が表示される。具体的には例えば、①製造や入荷の遅延、消費期限切れ在庫や停滞在庫の発生など、現場への注意喚起や是正指示②受注・仕入れ・売上・作業時間の実績や標準原価との差異など、経営層が見たい情報である。ユーザーごとに細かく権限設定することも可能で、工場の見える化がシンプルに実現できる。これらは、入力データが全てリンクしている統合型システムならではの特徴だといえる。
システムに対する要望
キリンディスティラリーでは、新システムの導入による主な改善目標を「発注ミスをなくすこと、担当スタッフの作業負担軽減を図ること」(原氏)に置き、その実現に向けてはローゼックに次のような仕組みづくりを要望した。
- 入力データをマスターデータとして一元的に登録・管理でき、エクセルのようなシート、ブックごとのデータのコピー&ペーストが不要になること
- 納入指示書の版管理がしやすくなり、前回提出した指示書との内容の相違点を明示できること
- 消費期限は、サプライヤーが品質保証する「品質保持期限」と自社基準の「開封後期限」のうち、必ず短い方を選択して管理ができるようになること
- 各原材料・資材ごとの最大在庫数、最小在庫数を考慮したMRP(Material Requirements Planning、資材所要量計画)計算が行えること
- サプライヤーごと、製造ラインごとの特性に合わせた柔軟な帳票出力
- 直感的な画面構成と単純な操作手順
これらの仕組みを実際のシステムに落とし込むというわけだ。
Q&Aシートの活用
システム変更による初期トラブルで工場を止めてはならない。ローゼックとシステム構築を支援する富士テクノロジーシステム㈱、そして担当スタッフは何度もミーティングを繰り返し、慎重に慎重を重ねた準備を進めた。その際に活用されたのが、表形式のQ&Aシートだ。
「こちらの要望や考えられる不具合、質問などに関して、ローゼックさんが文書で回答してくれるというものです。やりとりの履歴が残るので、質問のダブりや堂々巡りが防げますし、文書なので伝えたいことがより明確になります。ローゼックさんは私たちの質問に丁寧に答えてくださり、また難しい課題にも複数の解決策を提案していただけたのがありがたかったですね」(村上サブリーダー)
システム構築のプロも、こうしたコミュニケーションの重要性を強調する。
「どんなに実績を積んだシステム会社でも、実際にシステムを活用する製造現場との視点は異なります。そのギャップを埋めることで初めて生きたシステムになるのです。Q&Aシート自体は決して珍しい方法ではないのですが、今回の導入を通じて、現場から積極的に質問や意見を出していただくことの大切さをあらためて感じました」(富士テクノロジーシステム㈱ 営業本部 松原良雄部長)
既存の仕組みや関連システムも生かす
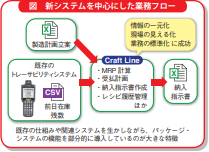
新システムは、ずは最も発注業務が複雑になるRTD製品原材料に限定して14年10月に運用を開始した。新システムを中心にした業務フローは図の通り。
「クラフトラインはもともとパッケージ・システムなのですが、可能な限り既存の仕組みや関連システムをそのまま活用できるよう、パッケージの一部の機能を使用するかたちで構築しました。従って、製造計画立案は従来通りエクセルを、トレーサビリティシステムも既存のものを使用できます。在庫管理データも別のシステムとひも付けしています」(㈱ローゼック 早川雅人社長)
このシステムを活用することによる発注業務は次のような流れになる。
- 生産計画数(エクセル)と前日在庫数をクラフトラインに取り込み
- クラフトラインでMRP計算
- 計算結果の確認と微調整
- 取引先との折衝と納入指示書の出力
- 入荷予定データを外部システムに出力
3時間が30分に
「原則、パソコン上では製造計画に基づいて計算されたデータを微調整しながら納入指示書に落とし込むだけの作業になったことで、それまで3時間はかかっていた発注業務が30分、つまり従来の6分の1まで短縮されました」(原氏)
この効果により、担当スタッフの残業時間は大幅に削減された。また、現在は消費期限や開封後期限、停滞在庫などの警告がホーム画面に表示されるようにしている。問題がないという状況を部署全体で共有できるため、担当スタッフにとっても、より安心感が深まったという。
「業務が複雑になるほど、人手ではどうしてもミスが起こりやすくなりますが、新システムの運用を通じて誤発注がない仕組みを得たという手応えを感じています」(山田部長)
変化に対応できる工場へ
実際に改善効果が得られたことを受け、今後は順次、新システムの範囲を拡大していきたい考えだ。
「当面は壜製品の原材料と資材で新システムが適用できるか検討を進めたいと考えています。すでにたくさんのミーティングを重ね、ベースは出来上がっていますが、最終的にどれを対象にするかは、物流上の制約などを鑑みて、システムに落とし込みやすいかどうかを判断して決めていきます」(村上サブリーダー)
多様化を続け、目まぐるしく変化する消費者ニーズに柔軟に応えていかなくてはならない飲料業界。製造現場に限らず間接部門を含め、工場はこうした環境の変化に合わせて全体で業務の最適化を図ることが求められる。キリンディスティラリーの発注業務スタッフは、そのことを身をもって経験し、改善に向けた一つの答えを見いだしたといえるのだ。
「お客さまに感動を与える企業として、これからもさまざまな製品をこの場所から発信し続けていきたいと思います。そのためにも、あらゆる変化に対応できる工場にしていきたいですね」(山田部長)