PDFファイルの表示はこちら。
通信販売のブレンド茶で国内トップクラスの出荷額を誇る「万能茶」を製造・販売する熊本県の㈱村田園。同社では現在、生産販売統合システムの活用による原価管理をはじめとした業務改革を進めている。「半月もかけて行っていた作業がなくなるかもしれない」。そんな期待も寄せられている取り組みの背景と中身に迫った。3世代で愛される万能茶
阿蘇の山々の麓、熊本県大津町に村田園の本社・工場・倉庫はある。熊本県は全国で4番目の栽培面積を誇る屈指のお茶どころ。創業者の村田正英氏はそんな恵まれた環境の下で1982年、茶の小売業を立ち上げ、当初は緑茶やどくだみ茶、くま笹茶などを扱っていた。
ある日、村田氏は地元客から「薬草茶にはそれぞれ効能があるけれど、それを一度に取れたらいいのにね」との声を掛けられる。同年、これをヒントに開発されたのが万能茶だった。その後は通信販売や口コミなどを通じてブランド化に成功し、現在、万能茶は同社の売上高の8割を占める主力製品となっている。
とうきび、はぶ茶、プーアル茶、甘草、霊芝など十数種類もの原材料で作られる万能茶は、これだけ多くの原材料を使用していても、健康茶特有の苦みや渋みがなく、すっきりとした味わいが特徴。
「発売から34年にもなりますが、おじいちゃんやおばあちゃんが万能茶のことを知ってくださり、お子さん、そしてお孫さんの3世代で愛飲いただいているというお声も聞きます。こうした声が私たちの大きな励みになっています」と語るのは、製造部工場長の河上清太郎氏。
2008~14年度の7年にわたり日本国内ブレンド茶葉通信販売市場の出荷額でトップ(㈱矢野経済研究所調べ)を獲得できたのも、こうした多くのリピーターファンによって支えられているからではないだろうか。
苦労して集計・計算しても生かされない情報
同社でのこれまでの原価計算は、あくまで財務諸表の作成を目的とするものであった。よって、原材料や資材の仕入れ価格、人件費、製造諸費など製造に掛かった全てのコストを、年度内に製造された製品数で割って原価を把握していた。
「いわゆる『全部原価計算』です。あくまで実際に製造した全量に対して原価がどれだけだったのかが分かるのみで、その都度変化する製品1個当たりの原価は出せません」と説明するのは、同社を担当する末永会計事務所の稲津好光氏。
こうした全部原価計算の下では、原価が前期と比べて高かったのか低かったのかは、期末になってようやく判明する。しかしながら、対象となるスパンが長いため、原価変動の原因を正しく特定するのは非常に難しい。せっかく苦労してデータを集め続け、計算しても、検証のための情報には生かされないというわけだ。
さらに、人が行う計数作業や計算にはどうしてもミスが伴いやすくなる。それが後になって分かったとしても、どこでどんなミスをしたのかを探り、一つ一つを修正するのは、決して短時間の作業で済まされることではない。
同社総務部の藤澤智恵部長は、「精査をするにも、毎回どこから手を付けてよいのか分かりませんでした。期末時の集計・計算には、ミスの修正を含めて半月ほどかかっていました。経理担当として、こうした状況を何とか改善したいとの思いは強くありました」と振り返る。
原価管理までできる統合システム
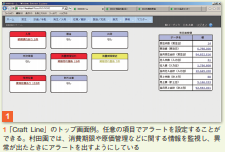
こうした原価計算の問題を根本的に改善するためには、原材料価格や歩留まり、作業効率の変動を反映した実際原価をリアルタイムで把握し、会社が設定した目標原価とのズレが生じた場合は問題の原因を特定できる仕組みが必要になる。
14年5月に本社・工場・倉庫が現在の場所に集約され、より情報の一元管理化が図りやすくなったことを受け、同社では同年末ごろから具体的な対策に乗り出した。そこで稲津氏が勧めたのが、㈱ローゼックの食品製造業向け生産販売統合システム「Craft Line」だった。
「雑誌かカタログでこのシステムを導入した企業の改善事例を見つけたことがきっかけでした。中小規模の食品工場でも導入できる価格で原価管理まできちんとできるパッケージソフトは、他には見当たらなかったのです」(稲津氏)
クラフトラインは、生産や販売、在庫、受発注、トレーサビリティ、製品原価など、食品製造・販売業務で必要となる各種情報を統合的に管理できるシステム。事業規模や業態、工場の管理レベルに合わせて段階的に機能を拡張できるよう設計されており、このため中小規模の食品工場でも多く導入されている。
特に注目すべき特徴は、業務の見える化に向けた各種機能で、例えば製造原価と標準原価との乖離や製造・原材料入荷の遅延、停滞在庫などが発生しても、リアルタイムで警告し、かつ社内で共有できる情報として示してくれる(写真1)。従って、何か問題があっても、直ちにその内容を把握・共有し、より迅速な対応が可能になる。
デモ用システムで便利さを体感
新システムの立ち上げに当たっては、藤澤部長と河上工場長、情報システム課の2人、またサポート担当の稲津氏の5人でプロジェクトチームが組まれた。クラフトラインの導入検討では、同社のレシピに基づいて仮組みされたデモ用システムで2カ月間ほど試す機会も得られたことから、確実に目的が果たせるのかどうかを含め、より具体的な運用イメージを膨らますことができたという。
「従来は決算期にまとめて手計算していた数値が、その都度、自動でさかのぼって製品ごとに出てくるようになる。それを体感し、システムを導入すると、こんなに簡素化されるものなんだなと驚きました」(藤澤部長)
新システムは15年5月に試験運用を開始。同年7月にはプログラムの修正を行うため一時的に停止したものの、その作業も完了、再度の試験運用を経て、今年5月には本運用をスタートさせる。
原価管理とトレーサビリティを同時に実現
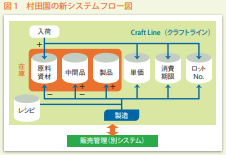
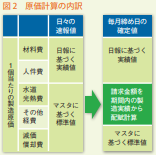
概略ではあるが、村田園の新システムフローを図1に示した。原材料の入荷時の情報(入荷数、単価、消費期限、ロット№)と、中間品や製品の製造日報の情報(完成数、投入数、歩留まり、作業時間)が同じテーブルに書き込まれているのが分かる。これが、原価管理とトレーサビリティを同時に実現できる理由だ。
なお、個別の製造原価は日々の日報から計算されるが、水道・光熱費については請求書に基づき後から配賦計算処理を行うようにしている(図2)。
財務分析にも力を入れていきたい
実務で改善効果を感じるのはこれからだとしても、半年に一度、およそ半月をかけて行っていた集計・計算作業は、この仕組みで確実に短縮されることになる。
「これまで、生産管理上の何らかの差異というのは、決算期になって初めて発見できるものでした。よって、その修正作業で膨大な時間を要していたのです。一方、新システムの下では日々の業務でこうした差異を発見し、その都度修正が可能になります。すると、半年ごとに行っていた集計・計算作業は事実上必要なくなることが考えられます」(藤澤部長)
統合システムであるクラフトラインでは、原材料の入荷情報や仕掛品、製品の製造情報をシステムに入力すると、在庫数の更新だけでなく、在庫評価額、レシピに基づいた原価積算、歩留まり計算、ロット№、消費期限など、関連するさまざまなデータ更新が連動して行われるため、異なるシステムへの二度打ちやコピー&ペースト、手書きによる転記作業が全く不要になる。たとえ単価の間違いなどが後から判明しても、データがつながっているため、再計算させればよい。つまり、過去の業務実態をいちいち追跡する作業は要らなくなるというわけだ。
「決算向けの集計・計算は日々の業務をこなしながらの作業となるため、どうしても通常業務の時間外で行わなくてはなりませんでした。これがなくなるので、今後はもっとクリエーティブな業務、例えば財務分析にも力を入れていきたいですね」(同)
業務の効率化が新たなチャレンジを下支え
原価管理を含めた業務実態の見える化が進む中、従業員意識ではすでに大きな変化が見られ始めているという。
「コスト意識に対する変化もその一つです。新システムを通じて原価の変動を肌で感じられるようになったことで、原材料料とその使用量、生産時間、完成した製品の一つ一つをお金に換算して考えられるようになってきていると思います」(河上工場長)
こうした業務改革は、同社の次なるチャレンジにも通じている。実は現在、万能茶に次ぐ主力製品の開発、また万能茶のバリエーション拡大などの計画が進行中だというのだ。
「新製品についてはまだ公表できませんが、万能茶は春夏秋冬で異なる原材料を加えたり、パッケージを変えたりする季節限定製品を追加していきます」(同)
新製品開発において、原価管理やトレーサビリティなどの精度向上もより重要になるが、藤澤部長はむしろ業務の効率化がこうした新たなチャレンジを下支えする役割を果たすようになることに期待している。
「従来は手間のかかる事務処理で縛られ、諦めていた挑戦がたくさんあったと思います。しかし、システムの活用で効率化が進めば、業務環境は大きく変えられます。その分、これからは販売促進や新製品開発など、より前向きな業務に力を注げるようになっていけたらと願っています」(藤澤部長)